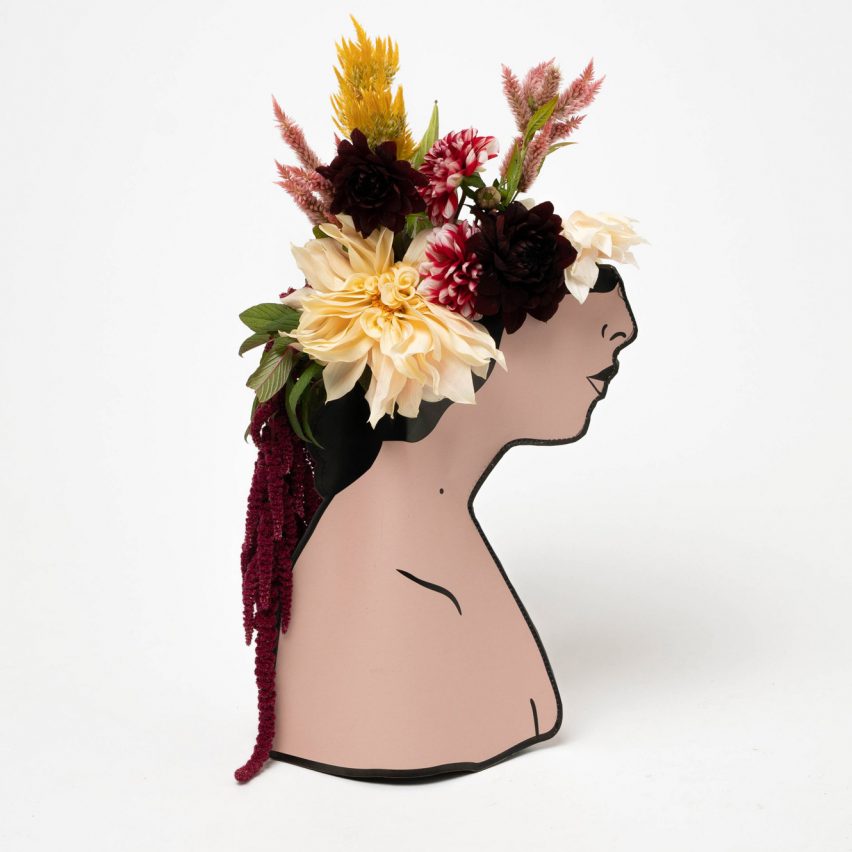
Design platform Exil Collective has launched its first collection at Dubai Design Week to spotlight work by both up-and-coming and established Lebanese designers.
Exil Collective's online platform features designs by over 20 independent studios in Lebanon, made by artisans and craftspeople that are also based in the country.
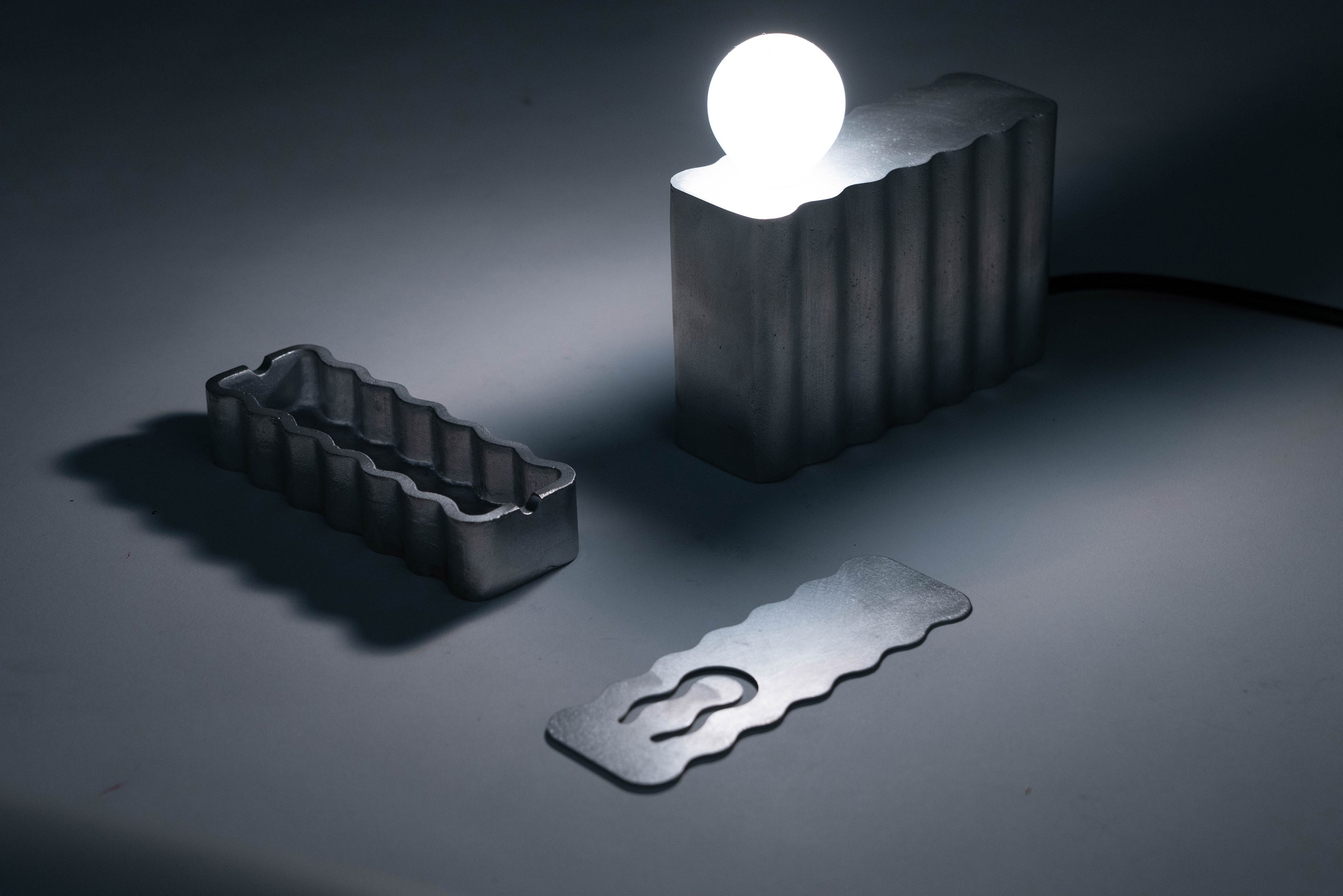
Among the products exhibited in the Downtown Design section of the 2021 Dubai Design Week were brass ashtrays and lamps by Youssef Bassil, sand-cast aluminium car sculptures by Antoine Guekjian and a globe-shaped, modular night light by Laetitia Jbeily.
"Exil is a bit of an incubator, which is the point because design in Lebanon is usually very expensive and luxury," co-founder Bassil told Dezeen.
"We wanted to break this mould, we wanted to invite designers from students all the way up to very established designers such as Marc Baroud."
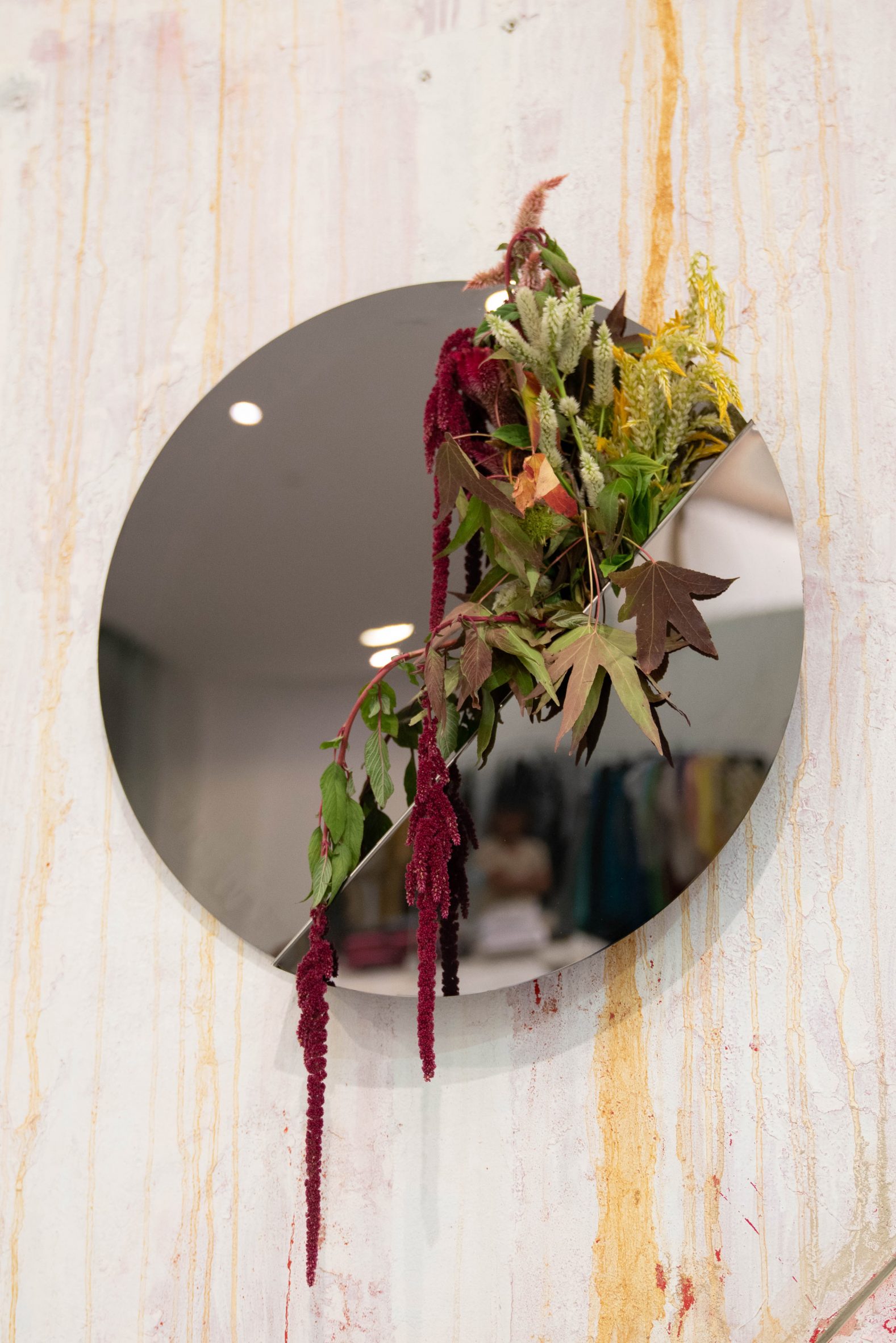
Each designer was given a spec sheet outlining the parameters for the weight, cost, materials and dimensions of the products so that the designs wouldn't be too expensive to ship when bought from the Exil website.
This resulted in pieces in materials and designs that aren't usually associated with Lebanon, including colourful tufted mats designed by RADCAT.
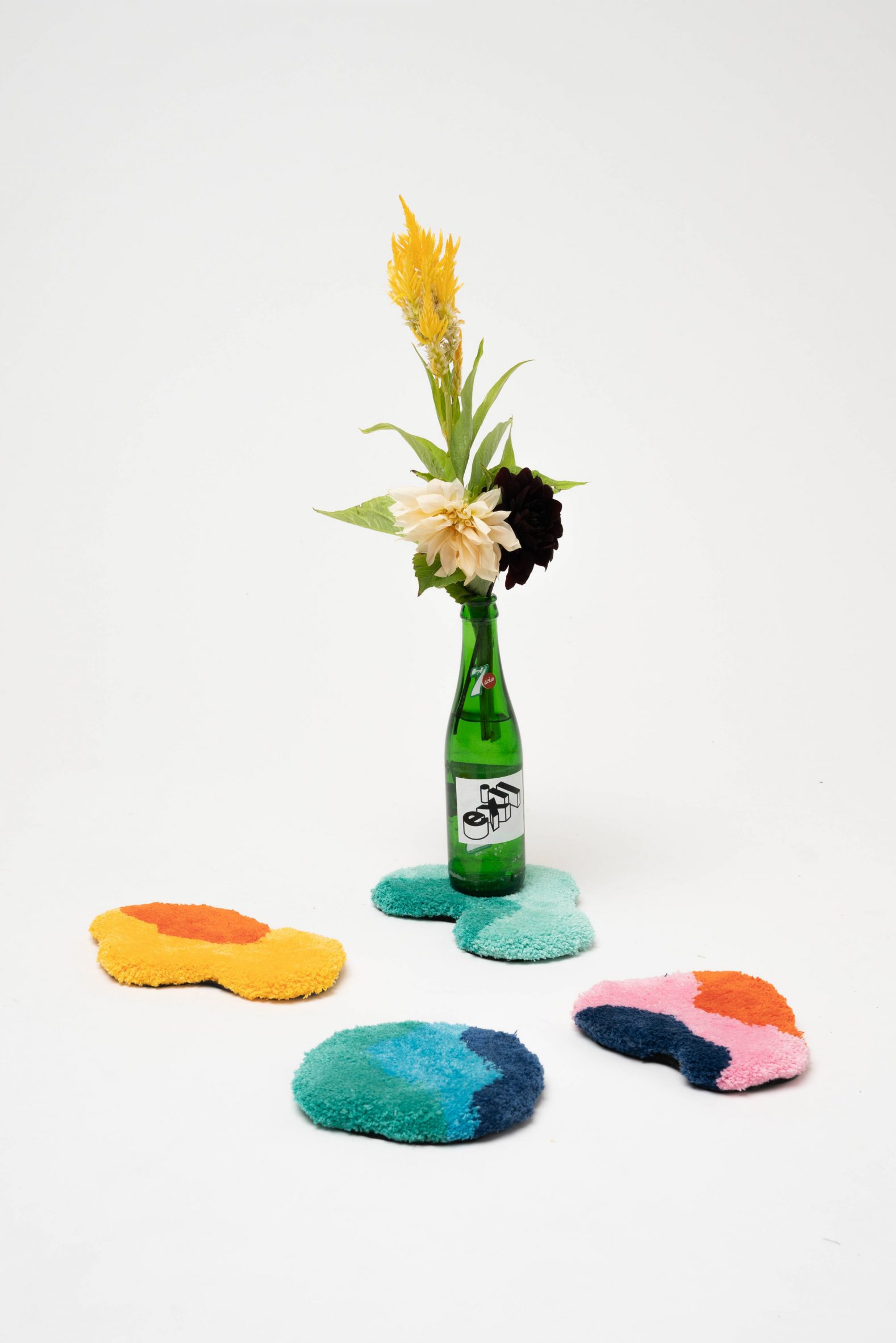
"The rugs, and the coasters that are also made from rugs; tapestry in Lebanon never really looks like that," Bassil said. "I think that was very interesting."
"And the metals and wood, very raw materials, that also shows more what's coming in Lebanon. We've got fantastic sandcast aluminium."
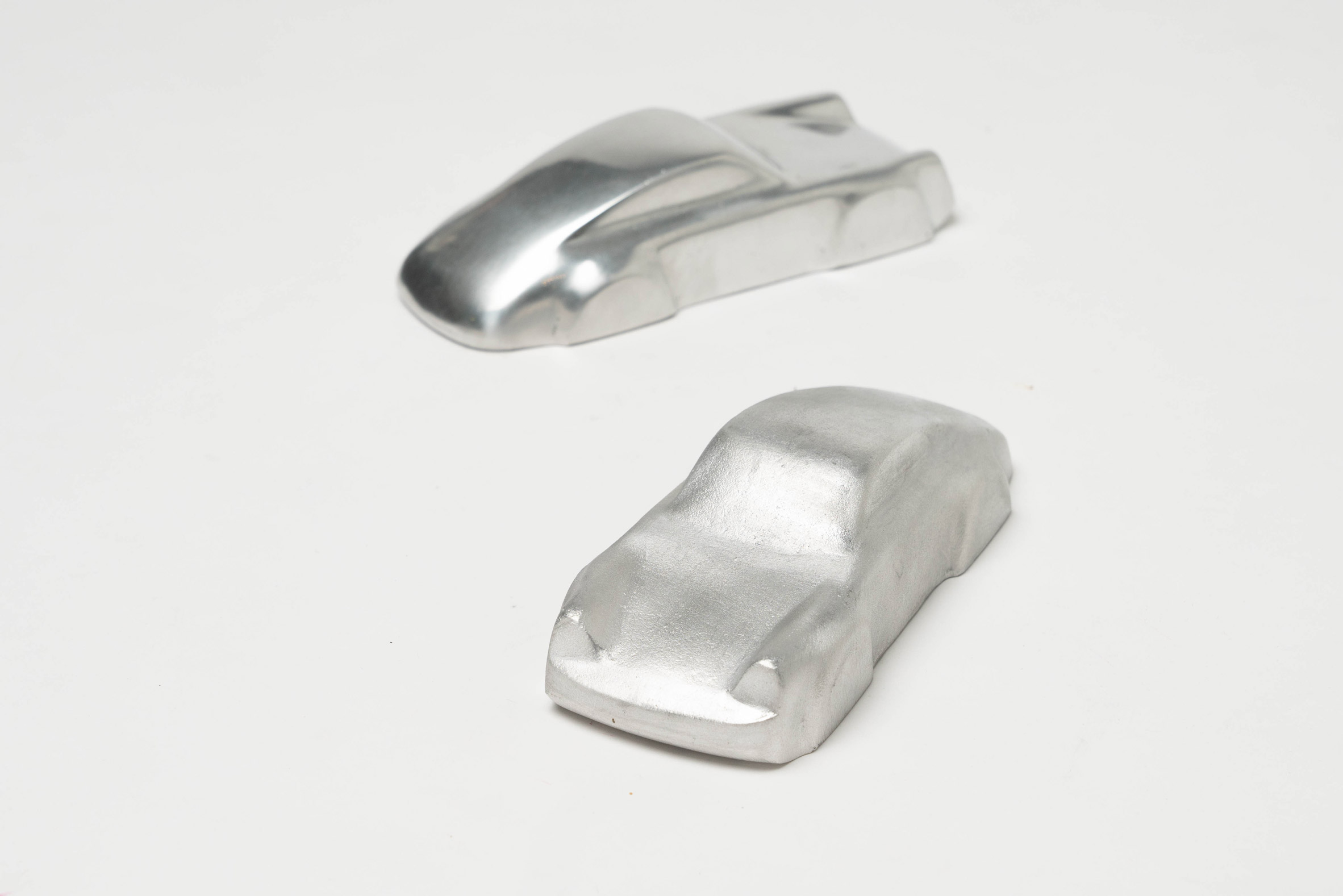
The pieces on show as part of Exil Collective were made by local artisans from a number of different fields, many of whom appreciated the challenge of working in new ways with the materials.
"Some of the artisans were surprised, as they're used to making larger pieces of furniture and one-off pieces – they're not used to creating repeated pieces that have to be consistent," Bassil said.
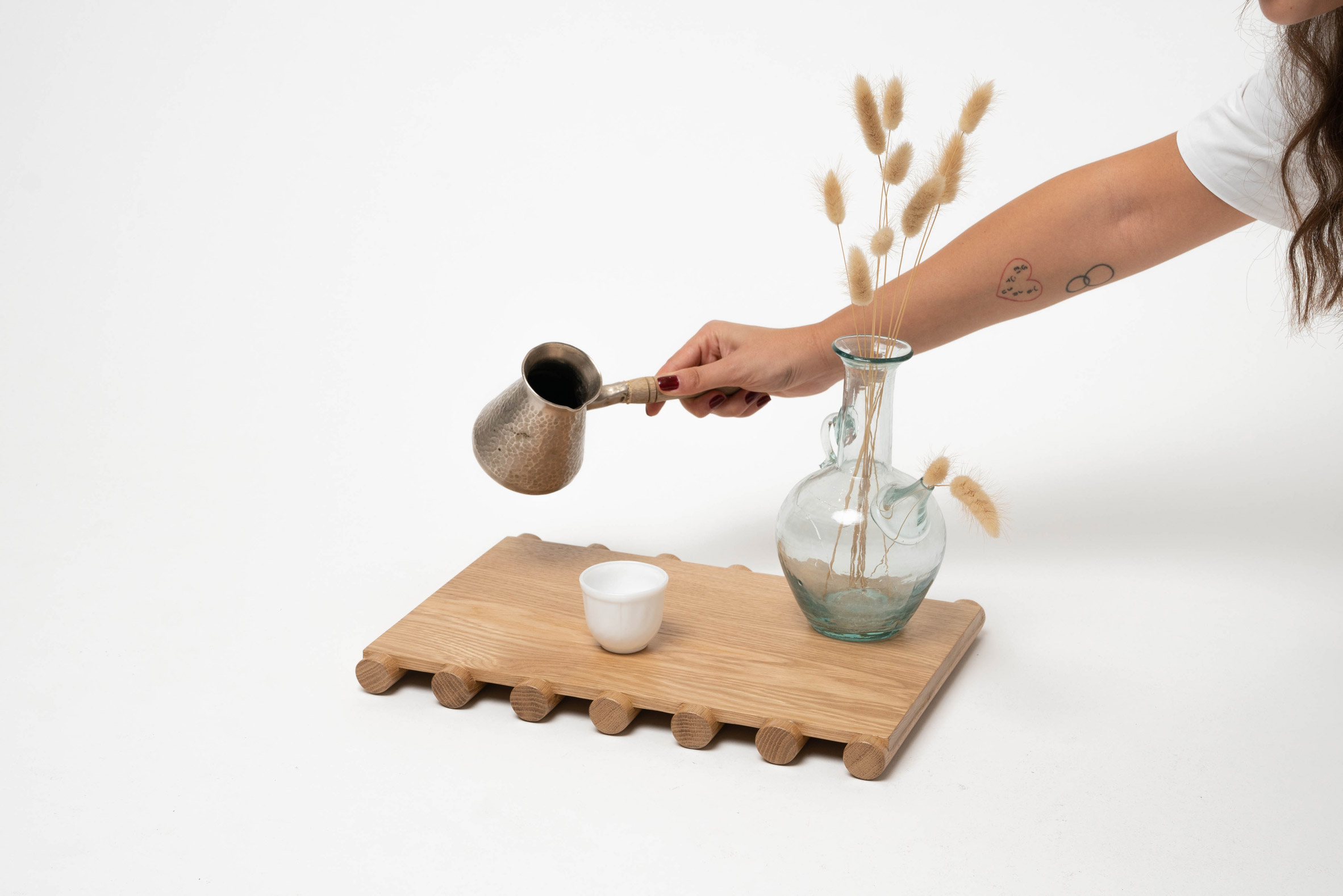
"Since the economic crisis in Lebanon is very tough, people want to work, and on top of that they were very excited to be working on something different and see the prospect of something that may be produced for the long term," he added.
The criteria set for the designs also created a line for the designers to follow, Bassil suggested.
"It's somewhat homogenous in its own way – it's very eclectic as well but there's something that connects it," he said of the collection. "It's all very simple and modest and you can feel the materials in the objects."
Exil Collective hopes the project, which was named Architectural Digest Middle East's Emerging Talent of the Year, will become a way for an international audience to discover Lebanese designers.
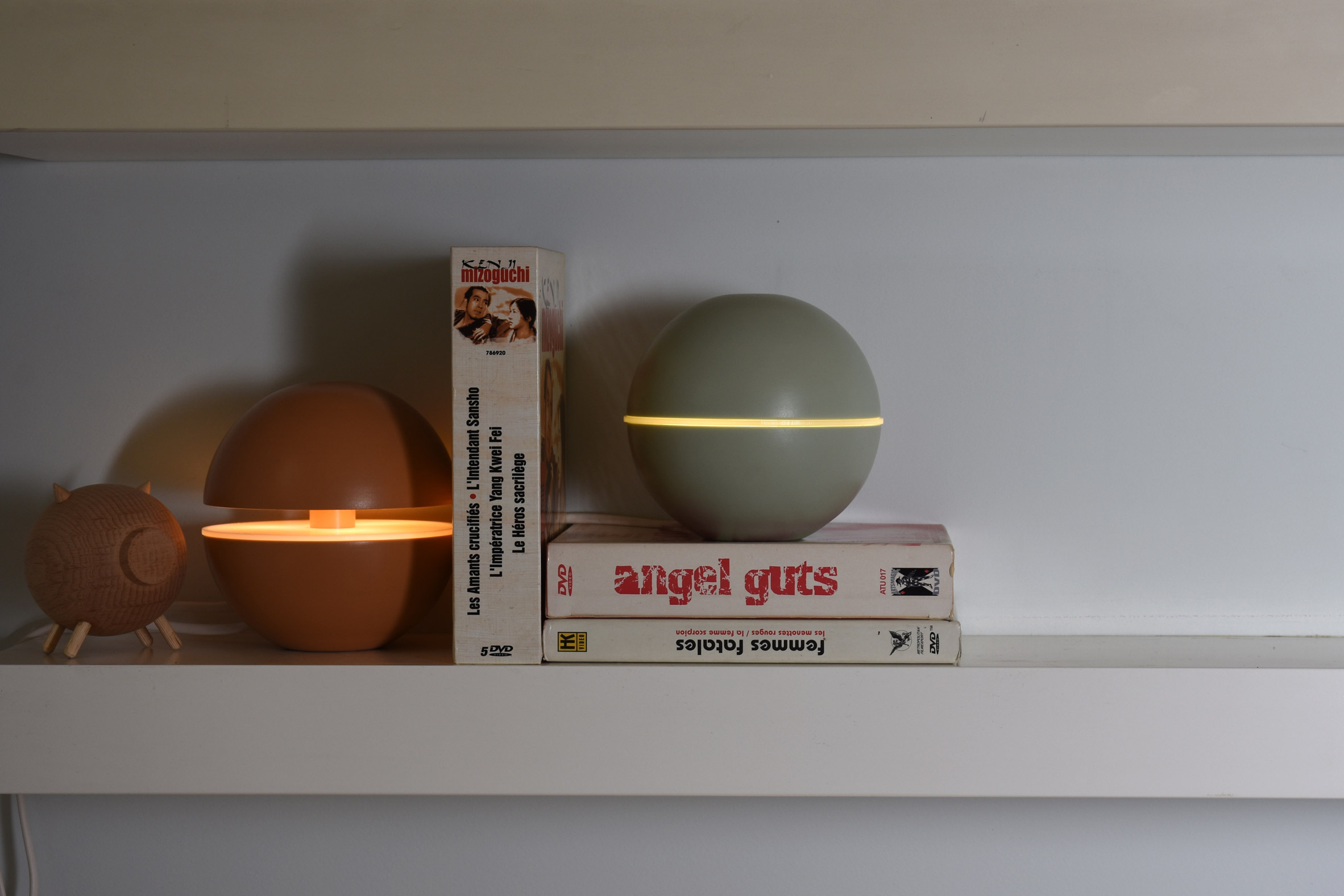
The thriving design scene in Beirut, Lebanon's capital, was severely affected by a devastating explosion that destroyed large parts of the city in August 2020. More than 60 international architecture firms donated artworks and drawings to help raise funds for rebuilding the city.
Earlier this year, Lebanese designer Khaled El Mays released his Transformers collection, featuring sofas and armchairs partly informed by the Transformers toys and films.
Dubai Design Week took place on 8 to 13 November 2021 in Dubai. See Dezeen Events Guide for an up-to-date list of architecture and design events taking place around the world.
The post Exil Collective showcases work by emerging Lebanese designers appeared first on Dezeen.
from Dezeen https://ift.tt/3GekEp8